2018..
Weld Reality Home Page 2.
WeldReality Training Resources.
THERE SHOULD BE LESS CONCERNS FOR MIG & FLUX CORED WELD PRODUCTIVITY, QUALITY, REWORK, REJECTS, RECALLS AND LIABILITY ISSUES, WHEN THE PROCESS CONTROLS & BEST PRACTICES AVAILABLE AT THIS WEB SITE ARE IMPLEMENTED.
|
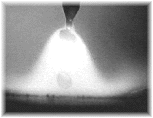 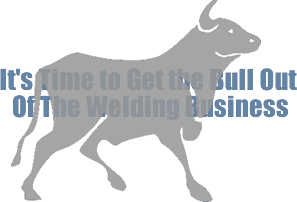 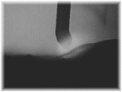
Please refresh this page as updates are frequent:
Management confusion about welder SKILLS" & WELD PROCESS CONTROL EXPERTISE:
When I am explaining to management or engineers why their personnel need Weld Process Control Training, a common response is, our guys dont need that as "most of the welders are highly skilled" and some have been welding for two decades or more.
They say this while we are both standing on the weld shop floor watch the weld or robot personnel "play around" with their weld controls..
Most managers, engineers and supervisors are simply not aware that manual welder skills has little influence on attaining consistent, optimum, manual and robot weld quality and productivity. You do not want to ask those exp manual welders to provide you with the weld data that a robot requires to make a common 3/16 fillet MIG weld with an 0.045 wire.
Optimum manual - robot welds are established through the primary weld decision maker's Best Weld Practices & Weld Process Controls Expertise. This is the expertise that I have taught for decades. This is the expertise that as of 2014, is still not taught in any global University or College that teaches Weld - Mechanical Engineers and Technicians. It's an expertise that since the nineteen nineties has been available at this web site.
The
following are a few of the companies that I generated dramatic
weld cost reductions through manual / robot weld process optimization.
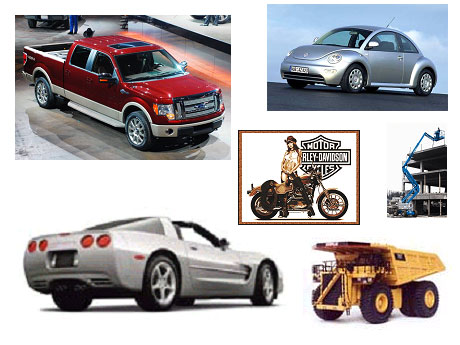
Ed optimized the above and many more robot - manual MIG applications.
Ed's Robot Weld Process Control Resources.
A FEW OF ED'S APPLICATIONS: Harley - GM - Corvette - Volvo - Ford / Chrysler - Subaru
- Volkswagen - Mercedes - Honda - GE - ABB-Westinghouse - Babcock - Textron -
General Dynamics - Imperial Oil - Combustion Engineering - Hydro Aluminum - Hayes
Lemmerz - Fruehauf Trailers - Case - Club Car - Genie - Sky Track - Manatowic
- John Deere - Caterpillar - Johnson Controls - Monroe.
With the common weld processes such as MIG, Flux Cored and SMAW, and the ever increasing, extraordinary amount of costly poor weld quality that is produced daily, the
potential for catastrophic
failures and product liability issues dramatically increases each year.
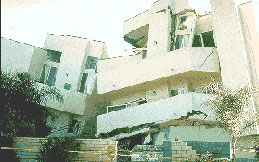
California and pathetic construction welds,
If anyone in the weld industry has doubts
about why anyone in this business should be concerned about the overall, poor, global MIG - flux cored weld quality and productivity,
they first may want to take trip to my "Bad Weld" section, and then also take a few moments to read about about the extremely poor self shielded (SS) flux welds that were responsible for many of the buildings
and bridges that toppled during the last
major earth quake in California. Most of the California structures were designed to stand erect during seismic loads, and these easily collapsed due to the use
of unsuitable Lincoln, Self Shielded flux cored wires, in combination with poor weld practices and
inexperienced designers, construction supervisors, engineers, project managers and welders, personnel who were
and likely still are not qualified to make sound weld process decisions.
The
year was 1984. I was asked to consult for one of the largest oil refineries in Houston. At the refinery, a new section
was about to be added. The pipe project required over a thousand pipe welds. At
the refinery, there was great resistance from both the engineers and project management
to using the cost effective, all weld position, Gas Shielded, Flux Cored wires.
In contrast, the this is the way we have always done it engineers, wanted to stay in their comfort zone and use the traditional SMAW (stick) process for the pipe
fill pass welds. The engineers were not concerned that the use of the gas shielded flux cored process, would
have created for their company superior weld quality with weld cost savings of approx. two million dollars for the project.
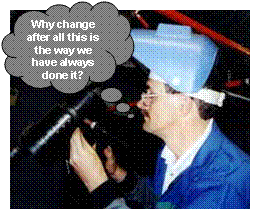
I don't suppose you ever heard the
above
statement from weld personnel in your fab shop.
IN THE CODE QUALITY WELD INDUSTRY THAT TYPICALLY WELDS PIPES AND PRESSURE VESSELS, YOU WILL HEAR
MANY MIG AND FLUX CORED WELD
OPINIONS, YET FEW OF THE OPINIONS ARE BASED ON WELD REALITY:
1984. In a weld report I presented to managers at one of Houston's largest refineries, I wrote the following: "On the subject of weld process quality and productivity optimization for your
new installation. During the weld meetings I attended
with your contractors, project managers and engineers, I hope you are aware that the managers and engineers that were the most vocal against the utilization of the highly
cost effective Gas Shielded Flux Cored process, were the least qualified in the meeting to have any opinion on any weld process".
Management and Liabilty Consequences from
Lack of Weld Process Expertise and Ownership.
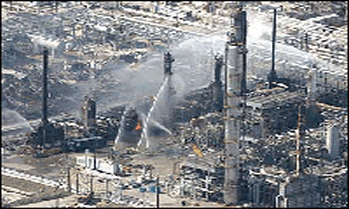
It's unfortunate that on the majority of major global weld applications, that few of the responsible managers and engineers have the weld process control knowlege
to daily ensure optimimum weld quality at the lowest weld costs.
Every
executive in an industry that daily deals with critical weld applications,
should ask the following fundamental question. Do
the managers, engineers and weld decision makers in our company, daily hold themselves fully accountable
for the quality of our products manufactured and do they also fully understand the equipment and processes utilized?
|
.
2015: THE COST CONSEQUENCES FROM INEXPERIENCED DECISION MAKERS..
During the last thirty years, those weld managers, engineers and supervisors who lacked MIG and flux cored weld process expertise, unfortunately drove up their companies weld costs and ensured that their
code quality, vessel
and pipe applications and their weld shop was stuck in a 1950 - 1960's TIG and SMAW process time warp.
|

2007:
You would be astonished to find that in the next decade, many global chemical
plants, refineries and power plants will be constructed using SMAW (stick) and the regular TIG process as the primary weld processes. The prime weld procedures
utilized to build these billion dollar projects today and in the last three decades were likely
in most cases based on the Stick and TIG weld procedures that were first established between 1950 - 1975. How many of the engineers at these projects gave consideration to flux cored and how many engineers knew how to optimize the flux cored process,
2007:
I wonder how long it will be before code quality weld projects wake up to the fact that for a few years now their is a much more cost effective, easier to
use pipe weld process that will attain superior manual and auto pipe welds than TIG - MIG or FCAW. This is a process that I partner and I bought to America, its called TIP TIG. For info, visit my pogram section or order the TIP TIG training program here.
THESE WOMEN QUICKLY REVEALED A FEW
FACTS ABOUT WELDING AND SKILLS:
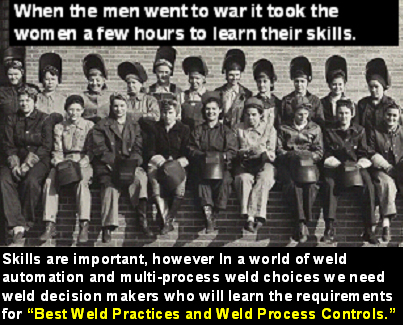
.
On
the left above, Ed is training American ship yard welders on how to reduce flux cored weld defects and optimize the flux cored and MIG welds without
"playing around" with their weld controls. In the middle, Ed shows Jesse, (age 11) that with less than 30 minutes of effective training, that it's a simple task to produce a code quality pipe root weld. By the way, thewelds were made on a
16 inch, Natural gas pipe supplied by Imperial Oil. On the right.
Ed training highly experienced Imperial Oil, SMAW pipe workers how to use and optimize their MIG
and flux cored welds for their field and shop pipe welds.
Wow I now sell weld gas mixes, this is better than
my last sales job at that the used car lot.
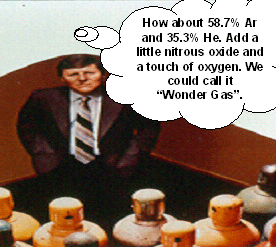
Perhaps
it's time for the captains and engineers of the weld industry to roll up their sleeves, rise up from their computers and step into the weld shop for more than five minutes at a time. While
in the shop, take a look around and ask this simple question. "What makes this weld shop better
than a good weld shop that was around in in the 1960s - 1970s" One good thing in 2018 would be for weld shops to cut their umbilical cords to their local weld sales rep for weld advice?
Here are the for real MIG Gas Facts.
There are many managers, engineers and supervisors that might want to take note: "weld
process & weld equipment ownership",
does not start with the workers on the weld shop floor".
In th
There are many managers, engineers and supervisors that might want to take note: "weld
process optimization & weld equipment ownership",
does not start with the workers on the weld shop floor".
In the 1980's, Ed was asked by inexperienced General Motors management to visit one of their plants to provide weld quality and productivity improvements. This was one of those plants in which the plant managers, engineers and supervisors spent their days in endless useless meetings trying to put out the weld shop fires. In this plant the managers and engineers lacked the ability to make weld decisions that had a positive impact for the weld production in the plant. It should be no surprise in this situation to find that the vast majority of weld decisions were left to the weld personell on the shop floor, thats the guys that daily "played around" with their MIG controls.
The following paragraph is from a weld report
that I provided to
GM.
For those managers that like to leave weld issue resolutions to the weld personnel on the weld shop floor, take note. As any weld manager or engineer should be aware, the welds on cars and trucks have tremendous weld quality, liability and productivity cost consequences.
Therfore an important logical responsibility for the managers and engineers involved with the manual or robot weld process is to take "OWNERSHIP of the equipment and processes" that can impact those welds.
The weld industry has evolved much more slowly than most other technical industries and as most are aware, few feel comfortable when major welding changes are desired. An important role for enlightened managers, engineers and supervisors is to be the catalyst to drive weld change that can improve either the weld quality or productivity.
ps: I know in the above GM plant that my weld report and views had no impact with the senior managers and engineers, which was no surprise to me, after all if these personnel were going to change, the whole GM corporate engineering and management culture would also have to change.
|
.
LEAN MFG. & ISO MEAN NOTHING WITHOUT WELD PROCESS CONTROLS & BEST PRACTICES.
It's common in global, large weld departments shops, to find managers who feel good about their newly qualified Six Sigma
engineers - technicians, or that they are especially satisfied with their recent implementation of the latest Lean Manufacturing craze from a weld process confused nation such as Japan. And of course, lets not forget all the time and money that these same managers may have put into their efforts to get and maintain that popular, and mostly useless ISO Approval, which has rules and regulations established by some of the most Bureaucratic organizations in Europe.
Logical weld managers - engineers and supervisors should never stray away from a simple fact. To consistently attain optimum weld quality at the lowest weld costs has never required Black Belts, Whit Shirts and Ties or Lean Mfg, and its never required costly ISO standards. Consistent optimum weld quality and productivity will be derived if the one person who daily makes the weld decisions has the necessary Weld Process Control and Best Weld Practice expertise.
IT COULD BE 1988, OR IT COULD BE 2018.
FOR MOST GLOBAL WELD SHOPS, MIG - FCAW PROCESS CONFUSION, PROCESS MYTHS AND PROCESS BS IS STILL THE SAME.
During 2014, many weld shop managers will decide to purchase that overpriced pulsed MIG equipment for their carbon steel and alloy steel welds.
I wonder how many of these managers will be aware of the primary pulsed MIG equipment weld issues and it's Achilles Heel which have not changed for almost three decades.
If you are one of those rare indiviuals that does not like to throw money out of the weld shop window, when you have a moment, visit the Pulsed MIG Welding
Section at this site. In the Pulsed MIG section, you will find a lot of interesting weld information about the extensive global sales BS that for decades has surrounded the pulsed MIG process and it's equipment.
For
those interested in providing cost effective, optimum quality
MIG and Flux Cored
welds, it's important that any weld decision maker;
[1]
has the ability to sort out the weld salesmanship influence from the weld process reality,
[2]
has attained weld process control and best practice knowledge from "qualified, unbiased" sources,
[3] has the ability
and desire to take process - equipment ownership,
[4] has the weld process control ability
to train and implemnt cost effective Best Weld Practices.
.
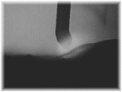
..
You would think that with construction projects and buildings designed to withstand the frequent California earth quakes, that an engineer should have certain
weld quality expectations for the structural steel welds made on the majority of those buildings.
Check out my California, Self Shielded flux cored weld farce article, and the resulting costly weld disaster for CA taxpayers.
The Northridge Earthquake Lincoln - FEMA weld Fiasco
For flux Cored ot TIG Process Control Training link here.
|
.
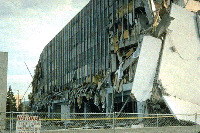 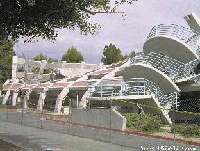
2007: Every day that City Hall, State or Federal Goverment - architects - designers and engineers allow the use of Self Shielded Flux Cored wires to be used on their construction projects. is a day in which engineering weld process ignorance reaches higher levels.
2014. THE SELF SHIELDED FLUX CORED WIRES USED IN 2014, ARE AND ALWAYS HAVE BEEN SINCE THEIR INTRODUCTION, THE WORST POSSIBLE WELD CONSUMABLES TO BE USED ON ANY PROJECTS IN WHICH WELD AND PART QUALITY ARE IMPORTANT.
The selection of Self Shielded (SS) flux core wires is common around the globe when constructing steel structures, yet the weld reality is these weld consumables should never seriously be considered for any code quality welds. Engineers and managers who are
often too busy to read my Welding Books and Self Teaching Programs, or read the Flux Cored sections of this site, will
however have the time to get weld process advice from a sales rep or from the companies who make the SS
weld consumables. And if a person does not mind BS the best process to start with in the weld industry is the SS process.
The wide use of the SS wires is again another example of lack of weld process expertise and a lack of management / engineering weld process ownership. For more info on why you don't use these wires, read below.
The North Ridge SELF SHIELDED FLUX CORED weld farce, would have made a good Tom Crusie movie:
READ ABOUT THE LINCOLN SELF SHIELDED FLUX CORED WELD WIRES AND THE UNUSUAL
LINCOLN FEEMA RELATIONSHIP. THEN FIND OUT HOW THESE WIRES INFLUENCED THE STRUCTURAL WELDING DISASTER AND REPAIR FIASCO THAT OCCURED DURING AND AFTER THIS CALIFORNIA EARTH
QUAKE?
If you are a weld manager or engineer and you accept your responsibility to ensure that the weld decision makers in your organization understand what is process - equipment - consumables BS, and what is real. I would recommend that you consider providing your weld work force with one of my process control
training programs, necessary to optimize the process
/ consumables utilized.
The weld industry daily pays a hugh price for weld process, weld equipment and weld consumable ignorance;
[a]
the weld shop daily weld scrap will be expensive,
[b] the weld shop daily weld rework will be costly,
[c]
the weld shop daily weld productivity will rarely be at it's potential,
[d] the weld shop weekly
weld team meetings will be time wasting, frustrating and fruitless,
[e] the weld shop employee moral will be low,
[f]
the companies weld failures and liability consequences could be dramatic.
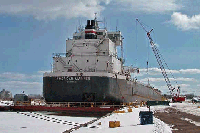 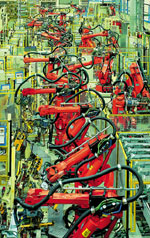 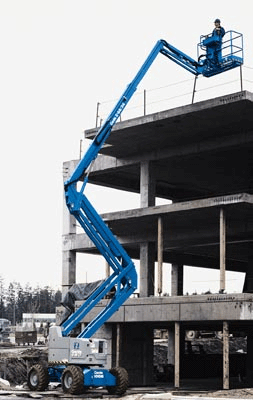
Question: What do the majority of ship yards and auto - truck plants and construction equipment manufacturers have in common?
Answer: They too frequently employ "hands off managers and engineers that don't believe or undersatnd weld process controls and weld ownership. These personnel therefore will typically lack the ability to implement Best Weld Practices and Weld Process Controls.
|
.
|