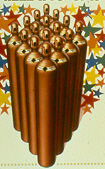
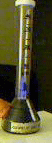
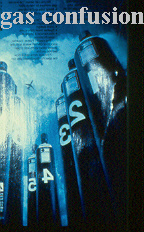
[1]
Welding with spray or pulsed: What weld parameter change would be required if
the welding shop switches from 95 argon - 5 oxy, to 80 argon - 20 CO2?
Answer:
[2]
Why does argon - 2 oxy produce cold, convex short circuit fillet welds on 10 and
12 gage parts?
Answer:
[3]
What MIG gas would you select for a spray transfer used for a multi-pass horizontal
¾ (18 mm) fillet weld on 326 stainless? And why?
Answer:
[4]
Why select argon - 2 oxygen, or argon - 5 to 10 CO2 gas mixes for robot spray
welds on carbon steels less than 1/8 (<3mm) thick?
Answer:
[5]
What are the fundamental welding differences between these two gas mixes, 97 argon
- 3 CO2, and 97 argon - 3 oxygen?
Answer:
[6]
Which of the following gases is most suitable for short circuit welding of 20
gage (0.035, 1 mm) carbon steel, and why?
[a]
98 argon - 2 oxygen. [b] 95 argon - 15 CO2. [c] 75 argon - 25 CO2.
Answer:
[7]
Which gas mix helps stabilize high current, MIG steel applications,
argon
- 5 oxygen, argon - 20 CO2, argon - 10CO2?
Answer:
Why?
[8a]
Why is an argon - oxygen mix unsuitable for MIG welding nickel alloy steels?
[8b]
May argon - CO2 be used in MIG gas mixes for nickel alloys?
Answer:
[8a] Answer: [8b]
[9a]
When welding low carbon stainless steels, why should you be concerned about the
CO2 content in the MIG shielding gas?
[9b]
How much CO2 is considered to be too much for low carbon stainless?
Answer:
[9a]
Answer:
[9b]
[10]
Popular gases for MIG welding carbon steels are argon tri mixes. These gas mixes
usually contain argon - 4/10 CO2 - 1/5 oxygen. A typical tri mix is argon - 2
oxygen - 8 CO2. Describe the welding difference you would expect between this
tri mix and a two part mix containing
argon - 10 CO2.
Answer:
[11]
You want to improve your MIG spray transfer carbon steel weld penetration on steels
> ½ (13 mm). Select the gas mix that will provide the best weld penetration,
and explain why you selected that mix.
Answer:
[12]
Select one of the following three gas mixes for your 3/8 (10 mm) carbon steel
application, to improve the impact properties of your spray transfer weld.
[a]
argon +2 oxygen. [b] argon +8 CO2 +2 oxygen.
[c] argon +15 CO2.
Answer:
[13]
What influence does oxygen have on the carbon content in an austenitic stainless
steel weld.
Answer:
Why?
[14]
Select an optimum, "single" gas mix that can be used for all carbon
steel and low alloy steel, MIG short circuit, pulsed and spray transfer welding
applications, and for carbon and stainless steels, all positions, gas shielded,
flux cored wires.
Answer:
[15]
You weld has excess surface porosity. How do you determine if the shielding gas
was the problem?
Answer.
[16]
how much helium can you add to an argon mix for "spray transfer" before
the arc becomes unstable?
Answer:
[17]
If it's ok to use 98 argon +2 oxygen for MIG welding a pipe, why is it not ok
to use the same gas to purge the pipe for a TIG weld?
Answer:
[18]
A weld shop uses 75 argon - 25 CO2 for MIG welding stainless steel, name the most
serious concern for using this gas on austenitic stainless steel.
Answer:
[19]
When added to argon for a stainless purge, hydrogen acts as a reducing gas. Why
is it a waste of time adding hydrogen to an argon MIG mix for this purpose?
Answer:
[20]
When welding a stainless steel pipe, when should the gas purging to protect the
root be stopped?
Answer:
Back to MIG Welding Gases