WELDREALITY HOME PAGE 4.
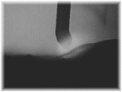 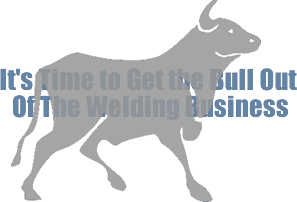 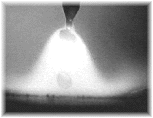
What you will find in home page 4.
Item: Their are weld issues in the plant and the management is again looking to blame the wrong person.
Item: The most costly pulsed MIG Lincoln power source versus the least costly CV Lincoln MIG power source.
Item: The Miller Maxtron and Invision helped put this wheel mfg. into Chapter 11.
Item: After introducing their new pulsed MIG equipment, most weld equipment manufacturers continuously made changes to the equipment without notifying their customers about the electronic changes and the resulting weld problems.
Item: Japan always the worst MIG equipment and auto - truck weld specifications that in many instances belong in Disney Land.
Item: Why purchase a costly pulsed MIG power source for gage metals, when the lower cost CV power source with short circuit is superior.
Item: Why purchase a costly pulsed MIG power source for welding steels > 1/16, when the lower cost CV equipment with spray transfer will provide superior weld fusion, less porosity, improved arc stability and often increased weld production potential.
|
Weld Management and
their sad
Umbilical Sales Cord:
.

When salesmanship has too much influence on a technical industry, that industry will daily pay an unacceptable price.
For
more than fifty years, the global, major weld equipment manufactures like Lincoln, Miller
and ESAB have been "MIG Process Impotent.
The reason we are a play around global industry is simple. The people whom make and sell weld equipment and consumables have for more than 50 years been unable to assist millions
of manual welders who still in 2012 "play around"
with their two control MIG weld process
The sad reality for the global weld industry, is when this industry needs weld advice, they constantly turn to the same weld equipment, consumable manufacturers and sales organizations that have proven over the decades that they lack weld process control expertise.
2012. For five decades I have been in this industry. I have seen little evidence of weld process evolution. Instead I see an industry that's on a fast paced treadmill that goes no where.

For more than four decades, the major industrial gas manufacturers
and distributors have been promoting
"three parts gas mixes" for carbon steels. In North Ameica, there are approx. 40
MIG 2 - 3 component gas mixes available, and Imn sure you will see an increase in the promotion of ridiculous four component MIG gas mixes.
The MIG gas mix weld reality for "carbon
steel" welds, is not one single weld benefit has ever been attained from a three
part gas mix.
For more than thirty years the major weld equipment manufacturers have promoted
costly, electronic pulsed MIG equipment for carbon steel welds. In all that time
this sensitive electronic weld equipment, has shown on the majority of carbon steel
and stainless applications, no practical
welding benefits. In contast in my 600 page Management Engineer's MIG book I have been able to write 60 pages of pulsed MIG , weld issues.
Next time you want weld application - weld equipment - process - and
weld consumables
advice,
consider the source.
10 WELD SHOP CONSEQUENCES FROM MANAGEMENT AND ENGINEERING,
MIG, FLUX CORED, ADVANCED TIG AND TIP TIG WELD PROCESS CONTROL & WELD BEST PRACTICE IGNORANCE:
[1]
Weld Process Ignorance has retarded weld process and consumable evolution, and dramatically increased weld cost and weld rework potential.
[2] Weld Process Ignorance can make weld automation more complex.
[3] Weld Process Ignorance can create
a confused weld shop culture and
numerous weld shop myths.
[4] Weld Process Ignorance closes the door to weld
equipment - process logic
and evolution
[5] Weld Process Ignorance opens the
door to weld salesmanship and the purchase of less than optimum weld consumables, useless three part gas mixes and costly electronic bells and whistles.
[6] Weld Process Ignorance creates a frustrated work environment influencing the weld shop culture and creating managers, supervisors and engineers
who will forever chase weld shop issues and never fully resolve them
[7] Weld
process ignorance hides the real cost of welds and places
weld cost focus on invoice
items like the cost of weld wires or the weld gas.
[8] Weld Process Ignorance is management, engineers and supervisors that are unaware of weld deposition rate
potential decreasing weld efficiency potential.
[9] Weld process ignorance ties up valuable plant personnel resources
who in useless meetings, waste valuable man hours trying to resolve weld issues
that should take minutes to resolve.
[10] Weld Process Ignorance dramatically increases a companies weld process liability.
Who do many managers blame when they see their
ROBOT WELD REJECT BINS FILLING TOO QUICKLY?
When
those robot weld reject bins fill too rapidly, many mfg, managers and engineers tend to blame;
the robot operators,
the robot programmers,
the robot equipment,
the robot weld equipment,
the robot fixtures,
the weld process,
the consumables,
the parts,
the salesman who sold the equipment.
However the weld reality is simply this. To solve weld process issues, and optimize
automated and
manual MIG / flux cored weld applications, both management and engineers should
have to take process ownership and attain the ability to recognize the "root
cause" of the welding issues.
Global Weld Issues & Weld Management - Supervision Responsibility.
This VP Manufacturing sends a message to the plant mgr. called Joe.
"For gods sake
Joe I don't want to hear any more of your BS on the subject of ISO and lean mfg. when you are unable to get the bloody robots outside your office door under control?
Joe, take a look around our manufacturing plants that are all making similar parts, yet for more
than a decade each plant has;
* used different weld consumables,
* used different size consumables,
* used different weld gas mixes,
* used different MIG weld equipment,
* used different weld data.
* used different robots.
The VP continues. "Joe, you know I believe in the "KIS" principle for our manufacturing plants. Two years ago when Ed Craig was here, he demonstrated that we have THREE PRACTICAL weld transfer modes available for all the manual / robot welds in our plants.
[1] Short Circuit Transfer.
[2] Spray Transfer. [3] Pulsed Spray Transfer
Ed who I believe is now Em also demonstrated to the managers, engineers, supervisors the results of his Robot Weld Optimization Training program and the quality and productivity benefits attained when those responsible for MIG welds fully understand the process and these 3 weld tranfer modes.
Remember
Ed taught us his unique. simple Weld Clock Method, and showed us that with three simple Weld Clock (wire feed) and Volt settings, that we could instantly attain the highest possible robot MIG weld productivity and quality.
I thought Ed's Weld Process Control - Best Practice training was great as it revealed that using the least costly, weld equipment and consumables, that our weld personnel that took the training did not have to even take notes to provide the optimum settings for the desired welds .
Joe, when I walked around
the plant today I wonder why Ed's training and practices was not ongoing. For example I noticed we have people in and out of the robot cells and obviiously playing around with weld controls. I can see from the fire works display in many robot cells that these robots robots are producing erratic globular type weld transfer, by the way this transfer is leaving difficult to remove spatter all over the parts and fixtures. Also I notice since my last visit we have been purchasing more costly
pulsed MIG equipment and three part gas mixes. What the hells going on Joe?.
The weld solution for many manager and engineers would likely be something like this. They request that the inexperienced robot weld personnel from each of their plants, create a global Weld Team, so that the inexperienced process control personnel can waste more time sitting around at meetings providing the wrong solutions to the daily robot weld issues.
VP Manufacturing finally gets it right and calls for another meeting with sad sack Joe.
"The bottom line is this Joe. As you know we have millions invested in our robot
weld lines, however before we decide to purchase one more robot I am making
it your responsibility to";
[a] Find
out and report back to me the common daily "root causes" of the plant's robot MIG welding woes.
[b] Then Joe I want you to provide the management leadership necessary to ensure all that all management
personnel, front office and weld shop floor weld decision makers are on the same bloody training path with Weld Best Practices & Weld Process Controls..
[c] Joe with that process control training, remember it includes all the managers, engineers, supervisors, technicians and QA personnel, also it would not hurt if the bloody designers of the welded parts understood the process that welds their parts..
[d] After the training establish effective, "VISUAL "
best weld mfg. practices for each robot cell.
[f] Lets not forget maintenance responsibility Joe. Please establish a weld, tooling, engineering and maintenance TEAM
that will react quickly and affectivily to the the issues influencing the welds.
[g] Finally Joe I want yo to ensure
that for each plant that the person with the most robot / weld process control expertise is the person thats "made responsible" for future robot / weld process training.
Few think
about
the influence and consequences of weld
Sales Advice
on the global weld industry:

With this pulsed MIG Lincoln MIG power source, I often saw RED.
On the left, a Lincoln Power Wave - STT, MIG power source. With the wire
feeder, MIG gun and a whole lot of other stuff I would never recommend. With this unit your company could
pay approx. $12,000 for
the privilege of producing a carbon steel MIG weld.
If
the Lincoln Power Wave was a car, I would likely place it at the bottom
of the list for performance, results and reliability. Also for the weld equipment repair costs
which you will likely incur with this type of equipment, you can anticipate equipment repair bills in the range of $2000 to $5000.
In contrast to the Lincoln Power Wave, the power source on the right is another Lincoln
MIG unit. This is the traditional, much more sensible Lincoln CV 300 amp MIG
package. This CV unit and similar CV package from Miller and ESAB, including a wire
feeder and gun typically sells in the $3,000 - $4,000 range. It's not a hard stretch to believe which power source
Lincoln and most weld distributors would rather sell to weld shops.
I have established MIG weld process controls in over
1000 manufacturing facilities in a 13 different countries. I have set up some
of the world's most complex automated and robot MIG weld applications. In all those weld
shops, with two pulsed MIG exceptions, when welding carbon steels and using a power source
like the above low cost, durable, Lincoln, CV 300 unit, I could;
[a] consistently produce the highest possible MIG
and Flux Cored weld quality
[b] produce MIG welds with the best weld fusion,
[c] produce MIG welds without spatter,
[c] produce
MIG welds made at the highest possible weld deposition rates and travel speeds,
[d] produce welds which would meet any global
MIG or flux cored weld code requirements.
You
payed 2 to 3 times more for that pulsed
MIG equipment and achieved what?
Pulsed MIG equip. = record
sales / profits for ESAB, Lincoln, Miller
and a new boat for the local weld distributor.
One thing a MIG power source should be able
to
deliver, is Stable Amps and Volts from a well designed Volt - Amp curve as found in a Miller Delta Weld power source..
|
Seeing
is believing. Hook up an arc data monitor to the majority
of today's costly pulsed electronic MIG equipment and evaluate the voltage and
current stability. Typically the much lower cost, traditional, CV, American Made MIG equipment
will produce higher(better suited) weld energy with superior weld parameter stability than any pulsed power source from
Asia, Europe, or the USA.
IF I HAD PURCHASED A MILLER INVISION OR MAXTRON POWER SOURCE, I WOULD HAVE FELT MORE THAN A LITTLE BLUE AND THE EXTENSIVE
WELD ISSUES GENERATED BY THESE MILLER MIG POWER SOURCES WERE MANY .
THE MILLER POWER SOURCE ISSUES WERE EXTENSIVE FOR A MAJOR USA WHEEL MANUFACTURER. A KEY ISSUES AT THIS WHEEL MFG. WAS THE PULSED ARC INSTABILITY
GENERATED WITH THE REQUIRED HIGH SPEED, WHEEL SEAM WELDS. FOR THE WHEEL MANUFACTURER, THE WELD COST CONSEQUENCES WERE GREAT.
When
welding steels, alloy steels or stainless steels, in contrast to the lower priced,
more durable Miller CP 302 power source, the costly, electronic, Miller Invision
and Maxtron offered less weld parameter stability and no practical weld benefits for the great
majority of steel applications. Of course if you listened to the person
who sold you this equipment you may have been fed a very different story. However if some one qualified
placed a weld shield over their face and evaluated the weld performance from
these power sources in contrast to the low cost, Miller CP 302 equipment, that would have been the
end of the story.
Workers don't buy weld equipment. The wheel manufacturing management and the engineers who were responsible for the purchase of the MIller equipment never understood a key manufacturing process that was critical for their organization. The reality is the apathetic management and engineers at this wheel mfg. drove the company into bankruptcy. It's ironic that after the bankruptcy, most of the management, supervisor and engineers were still not aware of their poor MIG equipment selection. More on the wheel story is found in the pulsed MIG section.
In 2012: If
a weld shop purchased the latest Pulsed Miller equipment to weld carbon steels,
it may have paid more than double the price of this traditional $3,000, Miller CP 302 power
source - wire feeder.
The Miller CP 302 is one
of my Best Buy recommendations for MIG welding steels
and alloys < 7 mm, and one thing it delivers with its good volt - amp curve is a stable MIG arc with a good balance of current to wire feed ratio.
FOR FOUR DECADES, THE TRADITIONAL, NORTH AMERICAN BUILT CV. MIG EQUIPMENT WOULD RARELY SEE THE INSIDE OF A WELD EQUIPMENT REPAIR SHOP. IN CONTRAST, PULSED MIG EQUIPMENT REPAIRS CREATED NEW OPPORTUNITIES AND PROFITS FOR WELD EQUIPMENT REPAIR SHOPS.
IN A THREE DECADE PERIOD, WITH ALL THE ISSUES GENERATED WITH THE PULSED MIG EQUIPMENT,
WHEN
DID YOU EVER HEAR A MIG WELD MANUFACTURER HAVING A PULSED EQUIPMENT PRODUCT RECALL. A RECALL THAT WOULD FIX THE ELECTRONIC ISSUES THAT THEY WERE AWARE OF IN THEIR FAULTY ELECTRONIC MIG EQUIPMENT. I GUESS AT THE END OF THE DAY, THESE WELD EQUIPMENT MFGS. BELIEVED THAT THEIR PROBLEMS ARE THEIR CUSTOMERS PROBLEMS..
Faulty
MIG weld equipment that provides inconsistent weld arcs from electronic components
can have extensive weld and liability cost consequences for a weld shop. Weld shops that
are using MIG weld equipment that does not perform in the normal operating range in
a consistent weld manner, would if the managers had the weld knowlege and two good balls, give consideration to seeking legal retribution
from the weld equipment manufacturers.
Every major MIG weld equipment company rushed their
pulsed MIG
equipment loaded with bells and whistles into weld shops without thoroughly testing their products.
With the proper testing and process knowlege, these companies would have been
aware that their
pulsed MIG equipment was
not quite right and at that time the equipment definately did not belong in a weld shop.
After introducing their new pulsed MIG equipment most weld equipment manufacturers continuously made changes to their pulsed MIG weld equipment
without informing their customers of the problems they found.
NOTE
TO MIG EQUIPMENT MANUFACTURERS:. PLEASE DON'T BE CONCERNED ABOUT THE ABOVE STATEMENT, LETS FACE IT, YOU ARE WELL AWARE THAT MOST OF YOUR WELD CUSTOMERS ARE NOT ASTUTE ENOUGH TO FIGURE OUT THE REAL ROOT
CAUSE OF THEIR DAILY WELD ISSUES. AFTER ALL, IF YOUR CUSTOMERS WERE PROCESS SAVVY,
THEY WOULD NOT HAVE PURCHASED YOUR PULSED WELD EQUIPMENT FOR THOSE STEEL WELDS IN THE FIRST
PLACE.
Thousands of dollars for paid for erratic
MIG
weld equipment performance:
This
weld current and voltage graph,
(black = amps, red = volts)
indicates the erratic weld voltage / current instability you may have recieved from
pulsed equipment utilizing the pulsed mode.
This graph was taken in Canada
by a technician who could not understand why he could not get weld consistency
on a simple, robot carbon steel application.
The volt amp graph reading was taken from a Panasonic MIG
power source. Similar results were also attained from the high end, pulsed Miller an Lincoln MIG equipment which had a price range of $6,000
to $12,000.
As noted in my books and training resources, one thing most weld shops are not aware of, is that with all MIG weld transfer modes, their is too frequently a poor ratio found between the MIG weld deposition rates, the resulting weld speeds and the weld energy generated. For example, with almost constant energy, CV MIG spray welds, you will often find that the weld fusion attained is marginal or lacking. So if you believe that the pulsed MIG process which spends 50% of it's time with a low back ground current of less than 100 amps is going to improve MIG weld fusion, then I have a park in the middle of New York I would like to sell you. Take a trip into my MIG weld equipment evaluation section, to see the superior performance attained from traditional, lower cost CV MIG equipment you typically pay less than $3,000.
The
weld reality is simply this. With a little weld process expertise that's attainable
from my
MIG /
Flux Cored training resources, the weld
decision maker would find that with the traditional, lower cost, more durable,
easier to operate, easier to repair MIG equipment, the highest "manual" MIG and flux cored
weld quality and productivity can be attained for the majority of steel applications.
A
MESSAGE YOU WON'T HEAR FROM GLOBAL WELD EQUIPMENT MANUFACTURERS.
This low cost, traditional CV MIG power source which has provided optimum weld performance for five decades, will on most carbon steel and stainless applications provide superior weld fusion and superior arc stability than any, more costly pulsed MIG, any Inverters or any multi-process weld equipment.
TO
FIND OUT MORE ON WHY THE SO CALLED EVOLUTION OF JAPANESE AND USA PULSED EQUIPMENT HAS BEEN A GIANT STEP
BACKWARDS FOR THE
WELD INDUSTRY Click
here.
When you cannot make the tools such as weld equipment any better, you may want to add bells and whistles that will greatly increase the price. Then add more process BS and lies so you further confuse your already confused customers. Examine the following typical marketing adjectives used to describe today's electronic MIG power sources.
Step right up folks, this new pulsed MIG weld equipment is better than Viagra.
Our new pulsed MIG equipment features will simply amaze you. We have;
ARTIFICIAL SYNERGIC INTELLIGENCE,
FOZZY WOOZZY,
SOFT/
HARD, HYBRID, DIP PULSED,
ETHERNET CONTROLS
WAVEFORMS BY THE MILLIONS,
ADAPTIVE
CONTROLS
RAPID ARCS
FTT, CDM
TECHNOLOGY,
PALM PILOTS.
2005: You want to produce a spatter free carbon steel or stainless MIG welds, well somewhere out their is a circus master, sorry I mean a Panasonic, Miller, Lincoln, ESAB sales rep looking for you. With the MIG equipment, arc monitoring test results that I witnessed in 2004, the MIG
equipment from Panasonic provided the greatest instability, Lincoln came a close second. The best pulsed welds
on steels that I witnessed from pulsed MIG equipment under $7000, was delivered by Daihen
- OTC pulsed equipment. The only steels application I viewed that benefitted from pulsed MIG was in building stainless MRI equipment. The thick walled, stainless vessels had extensive large sized welds and therefore were subject to distortion issues and pulsed MIG provided less distortion than regular MIG spray. MIG Process
control and optimum MIG short circ, pulsed spray settings for every applications are available in my process control self teaching and training programs.

Thousands spent and what benefits were attained
for those steel welds
?
If you MIG weld steels and wanted to purchase three
MIG packages and decided on equipment like the pulsed, ESAB Aristo, the
pulsed Panasonic HM 350 and the pulsed Lincoln Power Wave STT, MIG equipment,
you could pay approximately $30,000 for these three
units. Or purchase 3 traditional MIG packages like the Miller CP 302 or Lincoln
CV 300- 400 amp units for a combined cost of approx. $10.000.
With the lower cost MIG equipment, your MIG and Flux Cored welds will provide superior weld fusion and be more consistent. The conventional CV equipment should need less repairs and also be simpler to operate. With the thousands saved, you could spend a four hundred dollars and purchase a resouce that your organization needs.
Ed's Arc Weld Process Control - Best Weld Practices.
Japanese Manufacturing & MIG Weld Reality:
Japan
may make many of the world's best quality cars, yet "in-depth" MIG weld process expertise has for the last five decades been an even rarer commodity in Japan than it was in North America.
It's
not just the unnecessary electronically complex, Japanese MIG equipment that caused many
North American weld shops excessive headaches, the Japanese auto and truck weld
specifications that I have previewed, frequently provide comica, Disney Land type weld statements
and childish weld requirements, especially when welding thin gage, auto / truck carbon steel applications. With these applications you would find minimum weld fusion percentage controls were requested in the 25 - 35% range.
Most Japanese auto - truck MIG weld specifications are not based on real world manual or robot weld quality potential or weld logic, so the reality is the weld specs are rarely adhered to. I have to admit that I am ashamed to say that in 2012 this also applies to many of the the big three USA and tier one MIG weld specifications
that I have worked with.
THE
WELD SPECIFICATIONS - BEST WELD MFG PRACTICES AND THE WELD JOB DESCRIPTIONS PRODUCED BY AN ORGANIZATION ALWAYS
REFLECTS THE WELD MANAGEMENT / ENGINEERING PROCESS EXPERTISE IN THAT ORGANIZATION.
.
Japanese Weld mfg. Management and their often "lack of Weld Logic". |
.
To control their Japanese weld robots in USA manufacturing facilities, Japanese Auto and Truck managers typically request that Japanese weld power sources be utilized with their robots. Most of the < 2008 Japananese MIG equipment provided unstable weld performance and this equipment was a maintenance nightmare. The Japanese MIG equipment used with robots was so unreliable that If you did not have a spare Japanese MIG power source, you were in big trouble. Of course in a country that rarely used argon mixes and did not know what stable MIG spray or short circuit was, the inexperienced Japanese actually believed they could produce better quality MIG wires and power sources than the country that invented them. Truck loads of costly MIG wire and unstable MIG power sources was imported into the USA to feed the plants building Japanese vehicals, talk about the management and engineering logic of exporting poor quality coal to Newcastle.
TO ADD TO THE JAPANESE WELD PROBLEMS, THE JAPANESE MFG PLANTS IN NORTH AMERICA WOULD TYPICALLY NOT
HIRE AN AMERICAN TO BE IN CHARGE OF THE ROBOT LINES UNLESS THAT PERSON
HAD A DEGREE AS
A "WELD ENGINEER".
An important
fact that few most Japanese auto plant - engineering managers and HR managers did not understand. In
Asia, Europe and North America, the colleges and universities that provide weld
engineer programs, typically do not provide their future weld engineers with the
MIG best practices - weld process control expertise. This expertise is essential to consistently attain optimum weld quality - productivity. So while Toyota and Honda looked for weld engineers
in America, they ignored the simple reality that for the last three decades, the majority USA MIG welding robots have been controlled
by hands on technicians, these are the guys that had attained some experience.
Reference those argon gas mixes:
For decades after the second world war the Japanese had extremely limited access to argon, therefore this country did not know what a good quality stable, spatter free, MIG spray transfer weld was when used with specific argon mixes. Yet when the Japanese auto - truck companies came to America, these companies tried (and still do) to impose their inferior weld equipment and inferior weld methods on the US manufacturing plants. This again is simply another indication of the stupid global management that prevails in the welding industry, and of course a little of the Japanese "we are superior" culture had it's influence.
MIG weld robot issues will rarely be resolved by a welding salesman, by individuals with a black belt. or by engineers with a degree on the wall. And six decades have shown that weld resolutions do not come from the companies that make and sell robots, weld equipment and consumables. Robot weld issues will be eliminated once the responsible, key weld decision makers understand the levels of weld process expertise necessary for their own employees to achieve effective weld process controls. When this is done, management can finally take ownership for the weld processes they own.
.
A
fundamental fact
on gage steel applications and the use of MIG Short Circuit (SC) that is available from the lowest cost CV MIG equipment.
|
With
optimum MIG weld parameters that are simply derived from weld process control expertise and without the aid
of sophisticated, power source electronics, this 1980s slow motion video shot shows a MIG short circuit transfer weld on steel. The MIG power source used cost $1500.
Note:
Although the common CV power source has barely changed in the last five decades,
the 1980s slow motion weld arc shows consistent weld droplet transfer with no weld
spatter. The number one concern with gage < 1/16 steel parts is weld burn though. What makes a short circuit weld unique and ideally suited to thin gage is the SC arc is continoulsly in the On - Off mode. In contrast pulsed MIG is an open arc mode in which there is typically higher more constant weld energy. In 2005 North American MIG equipment manufactures are selling pulsed MIG power sources that
achieve no better results on steel gage applications for $5000 to $12,000
It's your choice, no process expertise and purchase expensive equipment, or apply
process control expertise and provide quality welds with low cost MIG equipment.
It's an ironic that while the conventional short circuit mode is a superior weld transfer mode for most carbon steel gage parts < 1/16, the weld reality is that most of the commom MIG equipment purchased in 2013 for both manual and robot sheet metal steel welds will be over priced, more complex, less durable more difficult to repair Pulsed MIG equipment. Extensive data on why SC should be utilized more frequently than pulsed is availabe in the short circuit section at this site and if you want to be able to provide maximum control of your gage welds. I recommend you take a look at these process control training resources..
.
A
Fundamental Weld Fact
on "MIG Spray Transfer".
On the left. The 1980s video reveals a slow motion shot of a MIG spray transfer
weld. The conventional MIG spray mode as it had done for
at least 50 years, can is set correctly transfer it's weld in a "controlled and consistent"
manner with miniscule weld spatter.
Note: The spray droplets may look
like pulsed transfer, however this spray transfer was from a low cost, $2500, traditional,
CV MIG power source. The reason this weld video looks like a pulsed weld is the MIG weld data
is set in the "spray transition zone", (weld parameters set between
short circuit and spray). Also the spray weld voltage is set a higher than normal to create a
longer arc gap so it can reveal the distinct weld droplet transfer. An increase in weld
current would decrease the droplet size and produce the traditional "spray
stream plus drop transfer".
In
contrast to what many weld equipment manufacturers or sales reps may claim. Spray
transfer from a traditional lower cost, more durable MIG power source, is superior
to the more costly pulsed mode for most flat and horizontal steels, low alloy steels and stainless
welds on parts > 4 mm, and parts that require stable high speed welds or welds with optimum weld fusion profiles and lowest porosity content.
How can MIG pulsed transfer provide superior weld fusion or less porosity than regular spray, when to create those pulsed MIG drops, the pulsed mode spends fifty percent of it's time at a low back ground current of typically less than 100 amps?
How can pulsed MIG provide more stability for high speed robot MIG welds when to transfer the distinct pulsed drops in an uninterrupted manner requires complex electronics to form the droplets?. In many pulsed MIG applications, you will find that the MIG equipmet electronics cannot keep up with the parameters or weld speed utilized or with the wire feed rate selected. In these circumstance when those moderate energy pulsed MIG drops make contact with each other they explode and add to the arc instability.
Note: For those high speed automated or robot welds arc length sensitivity can be critical to the stability and consistency of the weld metal transfer.
The
spray transfer weld stream in contrast to a pulsed MIG weld is much less sensitive to
arc length or weld parameter variations. The reduced arc length sensitivity benefit with spray is also beneficial when
welding steels with mill scale, coated steels or parts subject to magnetic field
issues. Extensive data on this subject is at the pulsed and MIG spray sections at this site and if you want to fully control your MIG spray and pulsed welds visit here.
THERE IS NOTHING MORE FRUSTRATING THAN DICUSSING WELDS WITH MANAGERS, ENGINEERS AND SUPERVISORS WHO CANNOT FIGURE OUT THEIR WELD COST POTENTIAL OR THE COSTS OF THEIR WELDS.
For those companies that today suffer from that infamous weld disease called, "Lack
of Weld Processitis", in these organizations, when the discussion on "weld
cost reduction" comes up, the management
focus is typically on something they can understand, like reducing the cost
of the weld wire (bring in the Chinease stuff) or discussing the cost of the MIG gas.
MIG
wire & MIG gas costs should typically account for 12 to 18% of the total cost of a
weld. Welding costs are primarily controlled by arc on time, weld deposition efficiency
and weld deposition rates determined by the wire feed speeds utilized.
Due to the general lack of management - engineering focus on MIG and flux cored weld process expertise, few weld shop decision makers
are aware of the weld deposition rates on the commom welds being achieved by their welders or by the robots
they walk past each day?
A WELD SHOP MANAGEMENT INTERESTED IN WELD COSTS, WOULD USE MY SIMPLE WELD CLOCK METHOD AND
A GLANCE AT THE WIRE FEED SETTINGS AND THEY WOULD BE AWARE OF THEIR WELD COSTS:
When
you have Weld Cost Confusion

you
have no control of the weld costs.
WHILE SOME WELD EQUIPMENT MANUFACTURERS MAY WANT TO SELL A WELD SHOP THEIR SO CALLED UNIQUE PULSED MIG EQUIPMENT THAT ENABLES MILLIONS OF WELD WAVE FORM COMBINATIONS, PLEASE BE AWARE THAT THERE ARE TYICALL ONLY THREE OPTIMUM MIG WIRE FEED / VOLT SETTINGS FOR EACH WELD TRANSFER MODE SELETED.
It's therefore reasonable to expect that managers, engineers and supervisors and technicians would want all their company weld
decision makers to be aware of the few CLOCK weld settings that Ed's identified, along with their weld application and weld deposition rate potential.
Don't
be the "weakest welding link" in your organization, follow these links to get control of your weld processes with Ed's MIG Best Practices - Process Controls - Weld Costs.

THAT LACK OF PROCESS CONTROL EXPERTISE & BEST WELD PRACTICE APATHY IN 2015.
In the USA this year, as it's been for decades, over 15Million Dollars will spent by Auto - Truck Companies for training, however I know that virtually nothing will be spent by these companies for
manual / robot MIG Weld Best Practices - Process Control Training. The bottom line is the type of training provided in an industry reflects the responsible managers / engineers expertise. Unfortunately, the majority of managers - engineers and supervisors in auto / truck plants don't seem
bothered if their robot MIG weld production does not meet it's daily production potential and the best possible robot MIG weld quality is being attained. The sad truth is is most managers today believe that MIG weld issues,rejects and weld a rework are simply normal functions that are to be expected from robots and the MIG weld process.
The
majority of large corporations that use robots in North America
have
spent
millions on implementing;
[a] international quality programs,
[b] lean manufacturing programs,
[c] ISO conformance.
Yet in these corporations manufacturing and quality
managers will daily walk by bins full of weld rejects and rework, watch their
weld personnel play around with weld controls and watch operators and unqualified
personnel make unqualified changes to the welded parts.
The
weld training programs available in Industrial countries too often focus on
weld skills rather than on the weld process best practices and process control expertise. All weld decision makers should have the ability to recognize the human, equipment, process and consumable root cause of their weld issues in both the
manual and robot weld applications. It starts with a management decision to purchase my low cost $400 process control program and then arrange a day in which that manager would sit his employees down and provide
them that program. My programs typically require 8 to 10 hrs and the changes in the weld quality and productivity produced in any weld shop will be both instant and meaningful.
A few hrs of MIG weld Process Control Training
quickly enables Robot Weld Production - Quallity Goals.
ONCE I PROVIDED THE ROBOT BEST WELD PRACTICES - PROCESS ONTROL TRAINING, I ESTABLISHED THE FOLLOWING GOALS APPROX 1000 MFG PLANTS IN 13 COUNTRIES:
With
robot MIG process control training, the realistic robot weld production and weld quality goals should be simple.
[] Attain no more than one percent daily
weld rework
from each robot.
[]
Produce robot welds with minimum spatter
[] Robot Weld Production: Attain
maximum robot weld speeds from
good programming and from the maximum weld deposition rates achieved per-weld.
[] Robot Down Time: With each robot cell, achieve less
than 20 minutes each shift for robot down time.
IT'S A SAD FACT REFLECTION ON THE GLOBAL MANAGEMENT / ENGINEERING PROCESS CONTROL EXPERTISE, THAT THIS YEAR AS IT'S BEEN FOR DECADES, A MAJORITY OF THOSE COMPANIES THAT USE MIG WELD ROBOTS AND DECIDE TO PURCHASE ADDITIONAL
ROBOTS, WILL NOT BE AWARE THAT IN MANY INSTANCES, THAT THE ROBOTS THEY ALREADY OWN WILL HAVE NEVER REACHED EITHER THEIR WELD PRODUCTION OR WELD QUALITY POTENTIAL.
Hopefully there are some weld decision makers and future weld decision makers out there that are getting the message on how to achieve these weld goals.
|

THIS EXHAUST MFG MANAGEMENT HAD REACHED NEW WELDING LOWS:
Could you believe that I in the 1990s I visited a large mid-west manufacturing plant that was making
exhausts, and all of the exhaust welds were made using the wrong MIG weld
polarity?
At the request of the absentee plant owner who was concerned about his never ending weld quality complaints, I visited this exhaust manufacturing plant, where the weld process issues and weld
quality cancer was so deeply ingrained that the plant management engineers and supervision were simply beyond hope.
I have also been in US plants and found the plants were welding their 400 series stainless exhaust components with carbon steels MIG
wires. In another plant, weld cracks were an issue as the employees were told to water leak test the parts while they were still super heated
from the welds.
Remember next time you purchase that
after market auto - truck exhaust, you may be glad its' not made in China and it was made in the USA. However three months later when that American manufactured exhausts fails or falls apart you may now be
aware of some of the prime reasons with the North American products. This too common lack of weld mfg expertise often made me wonder how the hell we managed to land a space ship on the moon..
AUTO
- TRUCK MANUFACTURING MANAGEMENT?
You
will note a large portion of the critique and advice on this site is directed at auto / truck
weld management. As
these industries have more welding robots than any other industry, it's logical
they should have more automated welding issues, however it's also ironic that in these plants you will also finf more engineers than most other industries that weld. An effective plant management would put these engineers to good use, that is after they first recieve the required process control training.
THE
FOLLOWING ISSUES, ARE AN INDICATION THAT MIG WELD PROCESS
CONTROLS ARE NOT PART OF A WELD FACILITY:
[1] If
the company has daily robot MIG weld rework of more than than 3% and robot weld down time of more than 20 minutes per-robot, per-shift.
[2]
If a company utilizes any "three part gas mixes" for carbon steels, alloy steels or
stainless.
Or if the company uses more than 3 different gas mixes in the plant.
[3] If a company believes they can produce superior carbon steel welds from
the
more costly "Metal Cored" wires.
[4] If a weld shop utilizes
gas shielded or self shielded flux cored wires for welding clean carbon steels < 3/8 (< 9mm) in the flat and horizontal
welding positions.
[5]
If the person who has full weld responsibility for the welding robots is an electrical
or mechanical engineer, or a maintenance person.
[6] If
the company allows operators or anyone other than the programmer to make welding
parameter changes to the robot program.
[7] If the purchasing personnel
at the plant make decisions on the weld consumables selected.
[8] If there is no "weld best practices - weld process control data posted on
the manual MIG wire feed controls or along side the robot cells.
[9] If the manual
welders have been instructed to use a whipping action or weave action with their
MIG guns.
[10] If the company uses pulsed MIG and the weld personnel are not aware how the pulsed arc characteristics or pulsed
weld deposition rates compare against the lower cost MIG equipment and the spray,
short circuit or controlled globular modes.
[11] If the company has more
than one manufacturing plant producing similar parts, yet the weld practices,
productivity and quality at each plant are different.
[12] If the weld
team has to meet more than once a month.
[13] If the maintenance department
personnel believes it's in the MIG gun repair business.
He
sets robot welds in the auto industry, we
have been told to cut out his"play
around organ"

How the weld shop culture and experiences can lead to
THE WELD SHOP PLAGUE.
THE YEAR WAS 2000 ROBOT WELD SALES WERE AT AN ALL TIME HIGH AND A WELD PLAGUE WAS QUICKLY SPREADING FROM
THE MANUAL WELD SHOPS INTO
THE NEW ROBOT WELDING CELLS.
In
a time when MIG weld automation has more focus than manual MIG welding, many weld
shops unknowingly spread their manual weld shop myths and diseases into
the robot welding cells. The
WE LACK WELD PROCESS CONTROL DISEASE that enroaches into the robot cells typically results in poor robot weld efficiency, more robot down time, poor robot
weld production, poor quality welds and unnecessary robot weld rejects / rework. Think about it, your arc welding
robots were not ill, confused or contaminated till they arrived in your manual
weld department.
Anyone
can "play around" with MIG equipment and make a weld without weld process
control expertise. However it's virtually impossible with robots or weld automation
to attain consistent, optimum weld quality and productivity without "weld
process control expertise", and the implementation of effective weld process controls.
There are few robots in manufacturing plants that are providing optimum arc welding quality or maximum robot weld production efficiency, and their appears few of the managers
or engineers that I met that had an interest in learning the requirements necessary for robot weld best practices - weld process controls".
Part of 1990s Ed Craig weld report delivered to Chrysler Corporate Management.
Note:
It was a wasted effort..
Increasing Robot Weld Production Efficiency.
To
reach their full robot weld production potential and minimize robot down time and weld rework,
managers and engineers have a few simple choices.
[a]
Retain the same inefficient weld production status and "purchase" more
costly robots".
[b] Add to the companies "labor costs"
by adding more manual welders to the robot lines.
[c] For less than the cost of a good dinner, provide their employee with
weld process control training as provided in Ed's programs.
It's
easy to understand why many people
outside this industry have poor perception
of the welding.
.
He sells weld equipment during the day and at
night he's the king.

It takes a lot of balls and not much else to dress like that.
.
.
.
.
|