Rev. 2018.
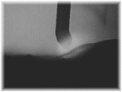 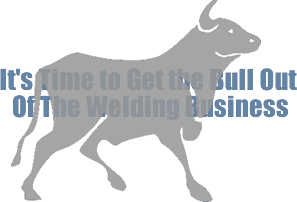 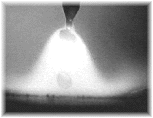
More on MIG - Flux Cored Weld Process
Controls & Best Practices:
.
The PULSED MIG Fiasco

It may come as a shock for those plants weld mostly steel and alloy steel applications, and invested in costly, (poor duablity - expensive to repair), pulsed MIG equipment, to find out that for approx. three decades that Ive been evaluating this equip, that the PULSED MIG weld equipment electronic BELLS & WHISTLES have provided minimal weld quality and productivity benefits for most steel - alloy stl welds, however these electronic features have for decades enabled greatly increased prices and profits for both the MIG weld
equipment manufacturers and distributors.
|
 
Thanks to the GLOBAL lack of MIG - Flux Cored weld process control - best practice expertise, in the past three decades, the majority of weld shops have thrown money out of their windows on the purchase of unecessary, costly, gas mixes and cored consumables that are not required, and also on pulsed MIG weld equipment that for most steel / alloy steel applications has typically been loaded with useless, electronic bells and whistles.
|
I would like to know another industry that for decades has relied heavily on biased,
unqualified sales influence to help resolve it's day to day technical, weld quality, productivity and weld cost issues...
For the last three decades, throughout the global MIG weld industry, millions of weld shops have paid 100 to 400% more than necessary to purchase a pulsed MIG power source. In the same shops they may also decide to waste more of their hard earned dollars by paying 2 - 60% more for useless three part gas mixes, or pay premium prices for unnecessary metal cored or flux cored wires. The solution to this unnecessary waste is simple. When the key weld decision makers in a weld shop have weld process control - best practice expertise, that expertise will be able to cut through the global weld equipment - consumables sales induced BS.
With weld process control expertise, the weld decision maker will have the important ability to provide the practical, cost effective requirements that are necessary to daily attain consistent, optimum weld quality and productivity,
and of course always at the lowest possible costs.
It's ironic, that in contrast to to the lower cost, traditional, CV MIG equipment, pulsed MIG equipment, multi-purpose MIG equipment, and MIG Inverters have for two decades typically provided inferior MIG and Flux Cored weld fusion profiles, higher weld porosity content and lower deposition rates for the majority of common carbon steels and alloy steels applications > 4 mm. The reason for these issues can are found at this web site and in
the MIG equipment sections, and of course in my weld process controls, best practices training resources.
The fear of a weld process or weld consumable change is natural on most weld shop floors,
and the fear will be exasperated when the relevant management, engineers, supervisors and technicians are not in full control of their weld equipment, processes and consumables.
|
It's not just "millions of welders daily playing around with MIG weld controls that is a primary concern for most weld shops,
it's also the hands off, management and supervision, and their reliance on sales biased weld process advice that is a concern.
This web site has a primary, repeating theme which is, "weld process control and best weld practice ignorance and apathy has influenced and created a common global weld shop culture, and that culture rarely likes to change the way it welds. In this environment, there is in many global weld plants, great opportunities for both weld quality improvements and dramatic weld cost savings.
How's your Weld Ownership - Weld Accountablity - Weld Expertise?
Imagine presenting the following
weld shop business plan to a bank manager.
|

Weld Ownership Accountabilty?
Management and Weld Consumables: Many weld shops in the 1980's were primarily utilizing the poor quality, poor productivity SMAW (stick) process instead of the more cost effective MIG and flux cored weld processes, and its a sad reflection that 30 years later in 2014, you can make that same statement. Also in 2014, many companies are using costly metal or flux cored wires instead of utilizing lower cost MIG wires.
Many weld fab shops, construction projects and companies that employ engineers that should know better such as the Chrysler Corporation, encourage the use of the obnoxious Self Shielded, (SS) Flux Cored weld wires. Apart from poisoning their employees with the carcinogenic, SS flux cored weld fumes, someone should point out to the ignorant management and engineers that allow the use of these flux cored wires, that when the SS process is used, it's almost impossible to consistently, enable optimum weld quality, or produce cost effective weld production on any weld application.
Management and
Weld Equipment Bells and Whistles: The
majority of electronics in today's MIG equipment offer limited real world weld quality or productivity
benefits when welding the common steel and alloy steels applications. However these MIG equipment electronics have on
average increased weld equipment costs by 100 to 600%, reduced the equipment durability and longevity and increased weld equipment
repair costs by at least 100 to 500%.
Management,
MIG Gas Mixes and Weld Consumables:There
are approx. 60 global MIG gas mixes available for MIG welding the common steels, stainless
and aluminium applications, yet the weld world needs only 4 gas mixes for optimum MIG welds
on every weld application.
How many managers this year know what the best four MIG gas mixes are? (Info in my MIG gas mix section). Also how many managers, engineers and supervisors will while looking for a solution to their daily weld shop issues. with advice from their local weld sales rep, try a more costly flux cored weld consumable?
Management and their Bigger Weld Wire is Better nonsense: There are many weld process ignorant managers, especially in the auto - truck industry, that believes that the bigger the weld wire utilized, the greater the the weld deposition and the lower the weld costs. As the weld current required for the large weld wires is typically not suited to the welds and the part thickness, that bigger is better weld wire is simply another old worn out weld myth. Its a sad weld reality that the majority of global weld shops have for decades been using the wrong type, the wrong size of MIG and flux cored weld wires, which goes along with the fact that they are frequently using the wrong weld gas mix.
After six decades running a weld shop should have managers like this.
In my 50 years in this weld business, I have
yet to meet two guys like these.
If most of the managers, engineers and supervisors that ran a weld shop
as if they had their own money invested in that shop, perhaps things
might have changed..
|
This company spent millions on robots and
fixtures and made welds like these on Ford Truck frames.
|